Data-driven manufacturing: unlock the power of your data
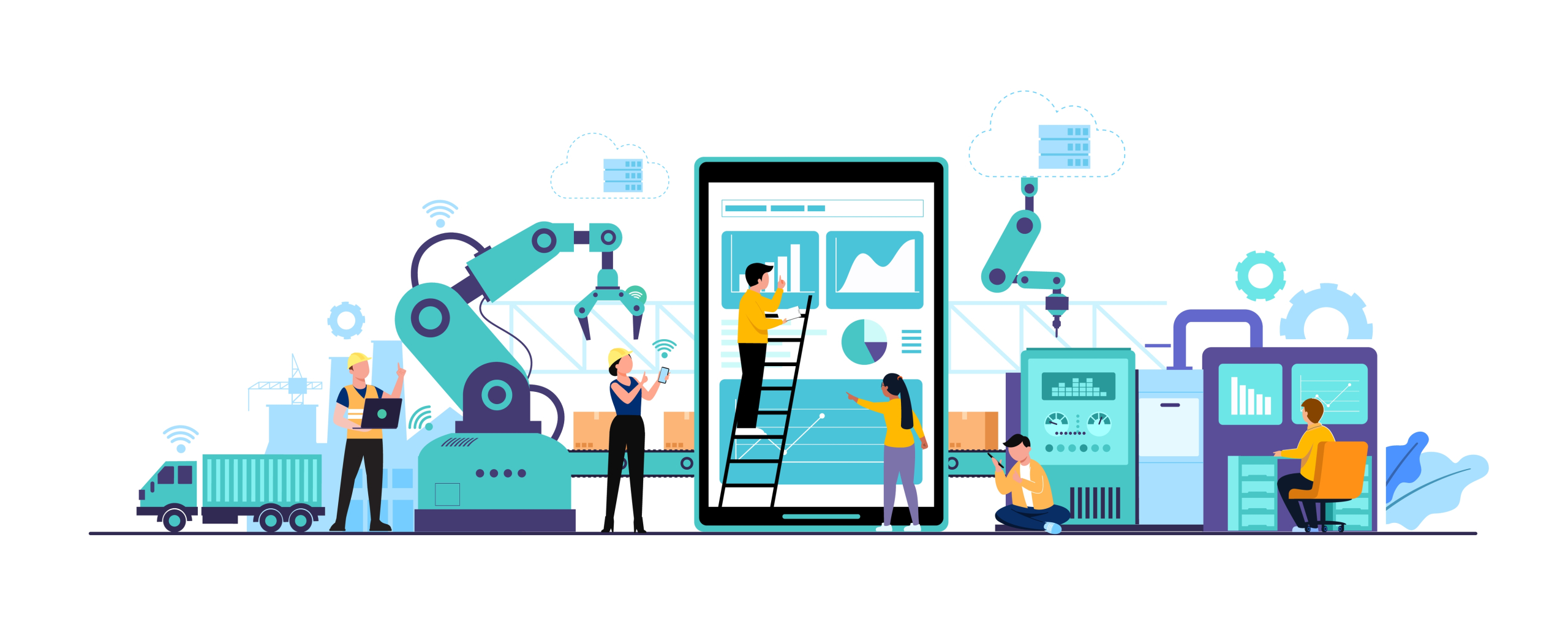
Technology enables the collection of vast amounts of information. Production managers must maximize its utility to enhance operations, boost productivity, and cut costs. Welcome to the era of data-driven manufacturing.
In this article, you’ll learn:
- what data-driven manufacturing is,
- how data is collected and processed in production processes,
- what the benefits of data-driven manufacturing are.
Data-driven manufacturing involves making decisions grounded in key performance indicators rather than relying on guesses or “hunches.” It also encompasses the concept of Industry 4.0, which integrates data from the shop floor, operators, the supply chain, and various other sources. This amalgamation enables manufacturers to make informed decisions aimed at reducing costs, enhancing productivity, and more through the utilization of intelligent products.
Data collection and processing
To effectively leverage data in your business, it’s crucial to gather it in a manner conducive to meaningful analysis. Additionally, it should be organized and made readily accessible to facilitate recurrent utilization by users. The objective is to prevent loss of the data gathered and maximize its potential utility. We’ve delved into this topic extensively in our article on data hygiene.
Consider the two scenarios: in the first instance, machine performance data is regularly stored in an XLS file. However, this data is neither publicly accessible nor fully secure. Now, contrast this with a situation where the same data is collected directly from the machines via the PLC, providing a highly accurate and uninterrupted data stream. This approach is a cornerstone of digital manufacturing, which leverages automated data collection to transform manufacturing processes through additive manufacturing, engineering informatics, and industry 4.0 technologies.
While both solutions are “data-driven,” the automated approach not only enhances security but also elevates the quality of decision-making processes by integrating supply chain management and machine learning applications for predictive analysis and manufacturability prediction.
Stages of using data in production
Collecting and utilizing data in a systematic and reproducible manner is invaluable for improving the production process. Achieving this can be facilitated by a process that encompasses three key steps:
- Capture and monitor data in manufacturing processes: Gather real-time data that is actionable and crucial for enhancing efficiency, productivity, and connectivity in machine shop control. Explore plug-and-play solutions that offer tangible insights into real-world metrics such as operational speed, hardware temperature, or power consumption rates, while also focusing on automation and end-to-end data visibility in manufacturing operations.
- Categorize and visualize data: Ensure that your data is structured and presented in a way that facilitates analysis. Explore a variety of solutions available on the market, including cloud-based options, that can integrate data from the shop floor. We’ve covered the available options extensively in our article on data integration.
- Analyze and act: Generate reports and analyze workflows to make informed decisions and develop strategic initiatives.
Benefits of data-driven manufacturing
According to the Fortune Business Insights website, the global smart manufacturing market is valued at USD 310.92 billion in 2023. It is expected to reach USD 754.1 billion by 2030. Industry 4.0 benefits from smart manufacturing, especially in these areas:
1. IoT and analytics
Large datasets in production enable the utilization of machine learning algorithms. Artificial intelligence and machine learning, coupled together, play a crucial role in enabling predictive maintenance through analytics, allowing for the early detection of anomalous behavior. This integration of artificial intelligence and machine learning assists in transforming additive manufacturing into a reliable and high-volume production technology. It develops machine learning-based solutions to expedite process development in additive manufacturing and uses machine learning applications to assist manufacturability prediction, predictive analysis of product performance, and microstructure simulation in the additive manufacturing field.
2. Automation
Automation can be categorized into two main areas: data collection and data utilization. Initially, the manufacturer automates data collection through data processing software. Subsequently, this data is employed in automated decision-making processes. Predictive analytics play a crucial role here once more: understanding past events, forecasting potential future occurrences, and executing appropriate actions.
3. Reduction of operating costs
Real-time data enables the monitoring of cost impacts resulting from any changes. For example, precision parts manufacturer Carolina Precision Manufacturing saved USD 1.5 million in one year by implementing an IoT platform, which enhanced data transparency and visibility.
It’s time to automate data management
Embracing data collection and utilization is a fundamental aspect of Industry 4.0. In addition, data-driven manufacturing optimizes operations, boosts productivity, and cuts costs. We urge you to unlock the full potential of your data. Our team is eager to assist you in revolutionizing your production through data-driven solutions. Don’t hesitate to reach out to our experts for guidance.